Tankerton Beach needed an upgrade of its coastal defences during the 1990s, funded by Defra this was possible in 1999 when Phase I and II was completed. Phase III was undertaken in 2003 and the defences are still in place today. The next scheduled maintenance is 2030 when the groynes may need replanking.
Background
Civil Engineers from Canterbury City Council carried out the detailed design of the new works and prepared the tender documents (drawings, bills of quantities, specification etc.). Due to different life spans of the then current groynes it was decided that it would be better value to stagger the works into phases. As the groynes at the eastern end of the bay still have a few years life left in them and are still retaining a reasonable amount of beach in front of the seawall. Initially the western and central thirds of Tankerton Bay, phases 1 and 2, were let as a single contract with an estimated value of £3.7 million. A second contract for the third phase at the eastern end of the bay worth around £2 million was let in 2003. The balance of the £7 million costs of the scheme are for maintenance works spread over the scheme’s 60 year lifetime, in particular the re-planking of the groynes in about 2030.
Mackley Construction won the contract for Phases 1 & 2 with a bid of approximately £3.5 million and commenced work on site in August 1998. Canterbury City Council required the works to be completed by the end of 1999, however the contractor finished by the end of October 1999. Despite a few periods of bad weather, the weather conditions over the duration of the works were generally favourable which, combined with efficient working practices, meant that the works were actually completed in mid-September 1999. This was three and a half months earlier than originally expected and six weeks ahead of Mackley’s programme.
Due to the varied nature of the works, Mackley elected to sub-contract some elements of the works to specialist subcontractors. The diagram below gives details of the various contractors working on the project:
Timber
As the timber used in the construction of the groynes is a tropical hardwood (Ekki), the City Council decided to purchase the timber itself under a separate contract from the construction works. This enabled the Council to ensure that it was supplied from an environmentally sound source. Wijma Kampon BV subsequently won the £340,000 contract to supply the timber pre-cut into the correct sizes from their forests and sawmills in Cameroon.
About 1,275 m3 of timber was needed for the construction of the new groynes. All the new timber was Ekki (also known as Azobe) which comes from Cameroon. It was chosen because of its good resistance to attack by marine borers and to erosion by shingle, much better resistance than any European hardwoods such as oak. The company with the logging concession takes its responsibilities towards the Cameroon forest, country and people very seriously and it goes as far as anyone in the quest for sustainable forest management. Only selected trees with a diameter of greater than 700mm are cut, leaving younger trees to develop and reproduce. Care is taken to ensure that the felling and extraction process disturbs the forest as little as possible. They do not practice clear cutting of the forests and the majority of the trees which are felled are sawn locally giving employment to the Cameroon people.
Even with these safeguards we wanted to use as little new timber as possible, so any planks and timber sheet piles taken from the demolished groynes which were in good enough condition have been re-used. It had also been hoped that it would be possible to re-drive some of the old piles. However, when this was tried, it was found that they had become too brittle and were splitting badly and consequently we were only able to use them as raking struts and strut ties. In the end about 13.3% of all the timber used in the construction of the new groynes and boat ramp was recycled. If all the timber used on the site were to be laid end to end it would form a line 52.7 km (32.9 miles) long.
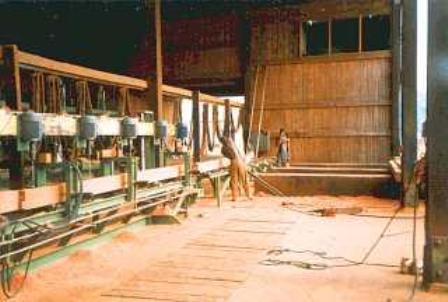
Construction works
Construction of the groynes commenced with the driving of the main piles. This was done using a drop-hammer piling rig with a muffled head to reduce noise. The piles ranged in length from 3m up to 9m, and each pile was driven at least half its length into the underlying London clay. In all, 1,455 piles were driven into the beach (total length 8800m, average length 6.05m). Once the piles were driven for a groyne, the timber sheet piles were driven into the clay and bolted to a waling plank.
After this operation the struts and ties, which give additional support to the groyne, were installed. The groyne planking was installed in two phases. The first was carried out after the installation of the struts and ties which brought the planking level a maximum of seven boards above the beach level. This is the maximum practical level for installing planking without temporary platforms for the workers to stand on which, due to the tidal nature of the work, are not very practical. This also minimised the risk of damage to the new groynes over the winter period. The second phase of planking was carried out while the new beach shingle was being brought into site.
Sea wall refacing
Approximately one third of the old seawall was in very poor condition and was refaced with 484m3 of concrete reinforced with 8,700 kg of steel mesh. In addition, some sections of the seawall were becoming undermined. To solve this problem, these areas were underpinned before the wall was refaced.
This work was carried out by a specialist concrete sub-contractor, HB Civil Engineering Ltd. The concrete was initially supplied by RMC and then later by Pioneer. In order to minimise surface cracking in the new concrete, fine polypropylene fibres were added to the concrete mix at the batching plant.
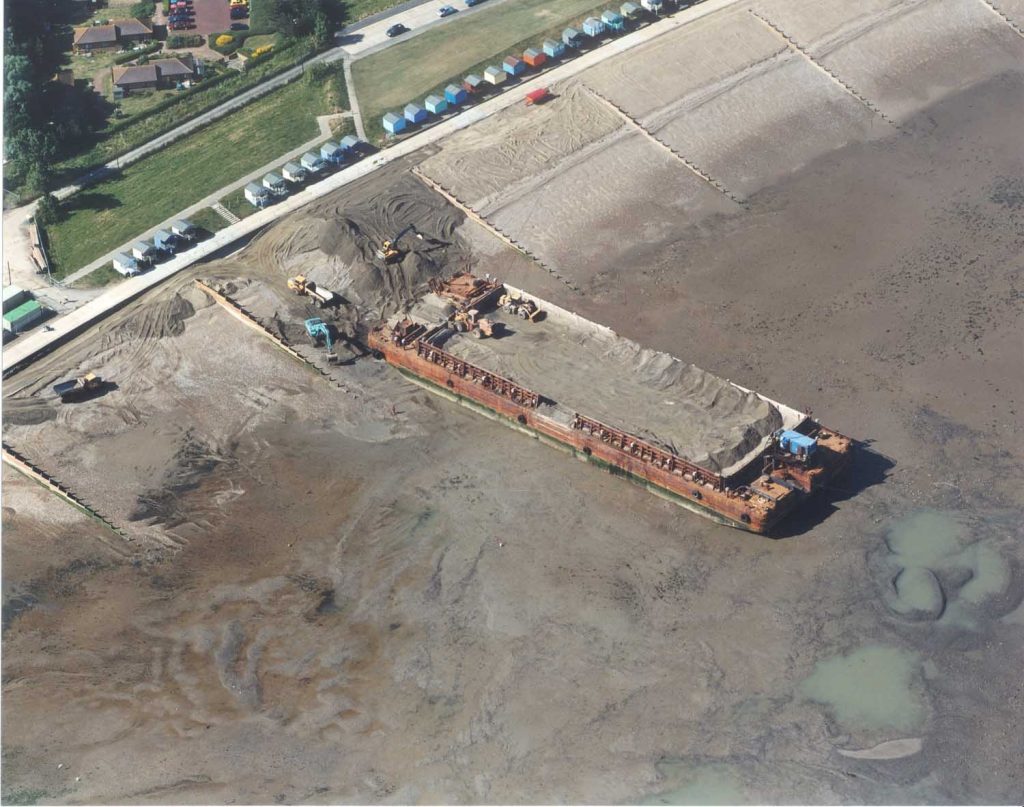
Beach replenishment
The old groynes were in very poor condition and were no longer retaining the shingle as intended. Consequently, the beach level was very low in areas and was not providing the necessary protection to the seawall. Once the construction of the new groynes was completed it was necessary to import to site approximately 130,000m3 of new shingle to bring the level of the beach up to the design level. The shingle was dredged from the Ministry of Agriculture, Fisheries and Food (MAFF) licensed dredging area off the coast of Hastings using a suction dredger.
With the amount of material needed, the logical method of delivery to site from the dredging area was by sea; otherwise around 10,000 truckloads would have been required. This would have caused significant traffic and environmental problems. The contractor elected to bring the shingle around the coast on board the dredger to a sheltered anchorage point near Reculver where it was transferred onto a flat-topped barge (approx. 90m long and 30m wide). The barge was then brought in to the beach by a tug while the dredger returned to Hastings for its next load.
Each delivery consisted of between 1,500 and 2,500m3 depending on the tides. The available depth of water at high tide can vary by over a metre between spring and neap tides at Tankerton and as the foreshore is very flat it was important to ensure the barge was not overloaded, otherwise it would run aground too far off shore. When the barge had been manoeuvred into position, a series of ballast tanks in the hull were flooded with seawater to settle the barge onto the seabed.
As the tide went out, the shingle was off-loaded from the barge by a large loading shovel which tipped the shingle into a pile off the front of the barge. Bulldozers and excavators were then used to spread the shingle into its final profile on the beach.